Comparison of different metering pump types
On the basis of abrasiveness and wear
1. Abstract
What characteristics are required of a metering pump that is to process highly viscous and abrasive media that are sensitive to shear with a high degree of process security and, at the same time, tolerate changes in the flow properties of these media? The solution: a metering pump in accordance with the positive displacement principle. A progressive cavity pump (PCP for short) is a well-known example of a pump of this type. A PCP combines the properties of pumping the medium with low levels of both wear and friction, resulting in a long service life and increased energy efficiency.
2. Introduction
In the electronics industry, there are essentially three different dosing applications: sealing with filled silicones or polymers, the application of pastes with very high filler content and the use of adhesives to join components. A large number of the fluids used in these applications contain fillers and these fillers affect the specific properties of the medium. They can affect thermal conductivity, surface hardness, electrical isolation, UV resistance, curing or gel time or thixotropy, for example. On account of their abrasiveness, these fillers make high demands of dosing components with regard to wear.
A number of different pump types have become established on the market:
- Peristaltic pump
- Piston pump
- Gear pump
- Progressive cavity pump
All of the above pumps work in accordance with the positive displacement principle (continuous or discontinuous). The factors determining the selection of a pump for a dosing application include the viscosity, chemical resistance and abrasiveness of the fluid, as well as the quantity to be applied per time unit and the required dosing accuracy. A simplified representation of the effects of wear and friction is set out below based on the concept of tribology. The tribological system according to the positive displacement principle is best represented as a siding abrasion system in which the particles are transported by the relative movement of the rotor/piston/gear (see Fig. 1).
3. Tribology of elastomers and plastics
The “tribo-system” of elastomers and plastics is described through the combination of the interaction between surfaces in relative movement and the environment. This interaction involves mechanical, physical, chemical, thermo-chemical and tribo-chemical reactions. As highly elastic materials, ViscoTec elastomers have been optimised to this effect. Their properties (e.g. excellent wear resistance and chemical resistance) are far superior to other polymers.
The pumps and dosing systems listed above can in theory cause three types of wear. For the sake of completeness, erosive wear is also described below.
- Abrasive wear
- Adhesive wear
- Tribo-chemical wear
- Erosive wear
Abrasive wear is the primary type of wear. It is the main factor determining the product life of elastomer and plastic components. Abrasion causes wear in the form of micro-fracturing and softening of the contact surface. The abrasion mechanism is influenced by many factors including friction coefficients, pressure, surface characteristics, sliding velocity, temperature, the modulus of elasticity and fatigue resistance.Adhesive wear is the type of wear that occurs between a surface (elastomer, plastic) and a smooth friction partner (e.g. metal). If the sliding velocity is relatively low, the surface of the elastomer or plastic suffers deformation (adhesive friction). Adhesive wear occurs if lubrication is insufficient, also caused by the medium.Tribo-chemical wear is a type of wear that is caused by the medium as a result of activation of the affected surface (elastomer, plastic) due to friction or a chemical reaction. “Layer wear” is usually started by a chemical reaction. Rather than leading to the sudden failure of the affected components, tribo-chemical reactions gradually weaken plastics and elastomers.
Erosive wear is a type of wear which results in material erosion due to the impact of particles against the surface of an object. If the particles are moving in liquid, this type of wear is referred to as hydro-erosive wear. It occurs primarily at high flow velocities.
4. Comparison of displacement pump types
The advantages and disadvantages of standard pumping and dosing systems are determined by the dosing medium (its viscosity, abrasiveness, chemical resistance) and the process parameters (delivery rate, accuracy, cycle time). Table 1 compares the various types of positive displacement pump on the basis of selected properties.
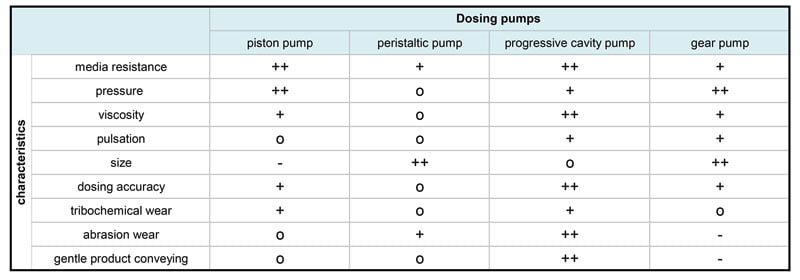
Gear pumps are suitable for applications that require uniform dosing. In the case of low viscosities, the pump tends to leakage flow and erratic volume flows when back pressure occurs. Media with medium to high filler content cause high shearing of the product on the contact surface of the gears, resulting in high levels of wear. Destruction and degradation of the fillers (e.g. hollow glass spheres to improve the flow) is thus unavoidable.
The advantages of piston pumps are to be found in their high dosing rate for virtually all media – from low to high viscosities. High pressures are possible thanks to their hard-wearing design. Piston filling times determine the cycle time of dosing applications. By contrast, endless dosing is only possible subject to restrictions or with a piston of the corresponding size. Here too, abrasive media cause abrasive or tribo-mechanical wear of the contact surface between the wall of the piston and the piston. The valve seats of inlet and outlet valves are particularly affected by this phenomenon.
Progressive cavity pumps are designed for dosing low to high-viscosity and paste-like media. Compared with the different displacement pumps, however, the eccentric worm pump is also ideal for dosing abrasive media. An even volume flow – generated by the endless piston principle – prevents sedimentation of the fillers at varying density. The relatively low pressures of 40 bar (compared with piston pumps and gear pumps) and the specially developed rotor-stator geometry reduce wear because there is very little shear in the flow, low to zero levels of pulsation and no return flow in the individual chambers. As a result, abrasive and adhesive wear is reduced to a minimum. ViscoTec is also able to counteract tribo-chemical reactions in the stator with elastomer compounds that have been developed in-house for chemically aggressive media. In conjunction with a special rotor link, the precision-manufactured rotor-stator combination optimises rollover properties and thus produces exact and accurate dosing results.
5. Wear types of the various pump types
6. Summary
It would be entirely inappropriate to categorise dosing pumps as “good” or “bad”. It is much more important to match the dosing system to the prevailing dosing requirement. Rapid, cyclic or continuous operation has just as much of an effect on the service life of dosing components as low to high-viscosity media and media with sensitive structures and high filler content. Tribological loss values such as friction force, leaks, wear, ageing and contact geometry affect the suitability of dosing pumps for specific applications depending on the medium used.
By contrast, chemical reactions affect the wear mechanisms in a pump (plastic deformation, abrasion, adhesion friction and fracture mechanics, for example). Often, dosing components can only be optimised for abrasive or chemically aggressive media by carrying out testing (including defined qualification testing) in advance. Finally, price will also be a factor in the selection of a specific pump. ViscoTec is continuously improving and optimising its dosing pumps in order to meet the increasing and changing requirements of the materials on the market. Much of our development work is in the area of materials research, focussing on chemical resistance and resistance to wear as well as functionality.