Adhésifs liquides : Les exigences envers la technologie de collage
Des défis pour les utilisateurs et les fabricants
Kleben schafft zuverlässige Verbindungen. Das hat sich mittlerweile in fast allen Branchen in den verschiedensten Anwendungen gezeigt. Doch die Anforderungen an die Verbindungsform steigen stetig. Und sie wollen auch in Zukunft erfüllt werden. Werkstoffkombinationen sind dabei der Schlüssel zum Erfolg. Hier kommt das Potenzial von klebtechnischen Verbindungen ans Licht: Denn nur mit ihnen ist es möglich, verschiedene Werkstoffe dauerhaft und unter vollständiger Erhaltung ihrer Eigenschaften zu verbinden. Die Vorteile dieser Technik kommen aber nur dann zur Geltung, wenn sie fachlich korrekt geplant und eingesetzt wird.
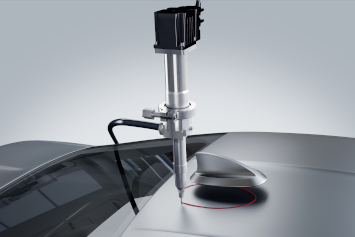
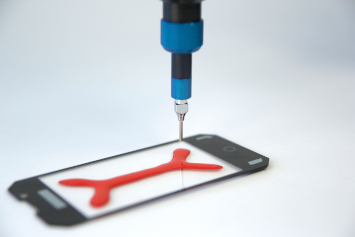
Les utilisateurs ou, même avant eux les fabricants, manquent souvent d’expertise pour pouvoir mettre en place efficacement des projets partiellement ou totalement automatisés. Beaucoup de variables peuvent contribuer au succès ou à l’échec d’un processus de collage dans la production automatisée : l’adhésif, le doseur, la robotique, le système de convoyage, la programmation, l’environnement, etc. Et de nombreuses variables peuvent également jouer sur la qualité d’une application de colle : l’aiguille ou l’embout du doseur, la vitesse d’application, la quantité à doser, la viscosité de l’adhésif, les bulles d’air et bien d’autres encore. Ce Livre Blanc de ViscoTec vous donnera un bref aperçu de certains obstacles que l’on peut rencontrer lors de la conception des systèmes de dosage et lors de l’application d’adhésifs liquides et la façon dont on peut les surmonter.
Le premier défi consiste à trouver le bon adhésif pour le projet en cours. Le défi suivant est : quel système est le mieux adapté pour appliquer l’adhésif ? Comment la technologie de dosage peut-elle être mise en œuvre de manière la plus rentable, mais aussi la plus efficace, dans une chaîne de production déjà existante ? Si ces points importants ne sont pas respectés, des retards de production, des coûts supplémentaires ou des défauts de qualité dans le processus de collage peuvent rapidement survenir.
Types d’adhésifs liquides et exigences particulières
Les ingrédients de base des adhésifs liquides sont les résines, les solvants, les durcisseurs, les charges et les additifs tels que les plastifiants, les antioxydants, etc. Il existe des adhésifs à prise physique et des adhésifs à prise chimique dit réactifs. Les premiers sont des adhésifs à un seul composant, les adhésifs à base de solvant et les adhésifs à dispersion étant utilisés dans le secteur industriel. Les polymères sont soit dissous, soit finement dispersés dans les solvants. L’évaporation du solvant entraîne la prise et la solidité de l’adhésif. Ces adhésifs ont généralement un temps de séchage plus long et doivent être protégés.
Avec les adhésifs réactifs, la structure polymère réelle ne se forme que pendant le durcissement. Les adhésifs réactifs mono-composant réagissent, par exemple, avec l’humidité de l’air ou la réaction de polymérisation initiée par la lumière UV. Dans de nombreuses applications, on utilise des adhésifs réactifs à un ou deux composants. Ils présentent généralement l’avantage d’une stabilité de stockage plus longue, car les éléments entrainant une réaction sont séparés les uns des autres. Les adhésifs réactifs à deux composants doivent être exactement mélangés dans le rapport de mélange spécifié, puis appliqués rapidement. Cela est dû au fait qu’ils n’ont qu’un temps de traitement limité, appelé « pot life », avant de durcir complètement. Le « pot life » peut varier de quelques secondes à plusieurs heures.
Plus les adhésifs durcissent rapidement, plus la chaleur libérée pendant le durcissement est importante en raison des réactions essentiellement exothermiques. Dans le pire des cas, l’adhésif surchauffe tellement qu’il peut endommager le composant. En fonction de la future plage de température d’application du composant, il peut être judicieux de faire durcir l’adhésif à des températures élevées. Ceci est important pour éviter des tensions ultérieures ou pour éviter un post-durcissement important. Le post-durcissement pourrait être associée à un léger rétrécissement, ce qui peut entraîner le cisaillement des broches des composants électroniques, comme par exemple dans l’industrie électronique.
Les systèmes de dosage de ViscoTec sont utilisés avec succès avec les types d’adhésifs mentionnés ci-dessus, c’est-à-dire les adhésifs à base de solvant et les adhésifs à dispersion. Et avec les adhésifs réactifs à un ou deux composants les plus divers, tels que les adhésifs acryliques, les résines époxy, les polyuréthanes, les polymères hybrides. Tout comme les mastics et les adhésifs, les colles à base de silicone et les mastics à base de polysulfure. Ils conviennent pour l’application de cordons, de points, de spray et pour le moulage de composants.
À quoi faut-il faire particulièrement attention avec les adhésifs ?
- Le temps de réaction – en particulier avec les adhésifs à deux composants – doit être adapté à l’application. Dans certains cas, on choisit des adhésifs qui durcissent si vite qu’il ne reste même pas assez de temps pour joindre les deux composants ensemble. Il en résulte une faible adhésion. Cette situation est aggravée par le fait que la colle est souvent jeté en raison d’un rinçage permanent indispensable pour nettoyer et libérer le mélangeur statique.
- Il est important de tenir compte de la dilatation thermique de l’adhésif et du composant. Souvent, même de petites augmentations de température suffisent à créer de fortes contraintes si la dilatation thermique est entravée. Pour certaines applications, par exemple en optoélectronique, il faut donc utiliser des adhésifs à faible dilatation thermique. C’est la seule façon de garantir un produit final de haute qualité.
- Les adhésifs à base de solvant sont généralement très inflammables ou peuvent dégager des vapeurs inflammables. Les solvants peuvent également provoquer des troubles physiques tels que des difficultés respiratoires, des vertiges, des irritations de la peau ou des yeux. Il est essentiel d’utiliser un équipement approprié pendant le dosage: aspiration, rinçage au gaz inerte, protection antidéflagrante, etc.
- Avec les adhésifs à un composant durcissant à la chaleur ou à l’humidité, il faut se rappeler que des interruptions plus longues peuvent provoquer un durcissement dans le système. Un débit de colle régulier est nécessaire ici. L’application est généralement effectuée sur un côté du composant. Les adhésifs doivent toujours être traités exactement selon les recommandations du fabricant ou dans les conditions ambiantes autorisées.
- Il est important d’éviter de l’humidité, en particulier lors du traitement des adhésifs à base de polyuréthane ou des composés d’enrobage. Le durcisseur pourrait réagir avec l’humidité et cristalliser. Même la résine une fois mélangée pourrait réagir et souffrir de cette humidité : Le dégagement de CO2 pourrait alors éventuellement entraîner la formation de bulles et de tensions.
- Lors de potting sous vide ou de l’évacuation ultérieure du composant enrobé, il est important que les différents composants du produit de coulée soient dégazés séparément avant le mélange et l’application. Sinon, l’air dissous ou les éventuelles bulles d’air dans les composants conduiraient à une forte formation de bulles et de mousse dans le composant. Cela entraînerait à son tour une contamination incontrôlée du composant.
En règle générale, le type d’adhésif à utiliser dépend fortement de sa fonction, de la température d’application, de la transmission de force nécessaire mais aussi du matériau ou de la surface des éléments à assembler. De même, la résistance des adhésifs aux influences de l’environnement dépend de nombreux facteurs.
Des défis spécifiques pour les fabricants
Déjà lors de la construction des composants, il faut tenir compte de la conception de l’adhésif, par exemple pour éviter les contraintes de pelage sur le collage et utiliser une surface aussi grande que possible. De la même manière, l’épaisseur du joint de colle doit correspondre au type d’adhésif ou vice versa. Pour de nombreux adhésifs, il existe une épaisseur maximale de collage, sinon la cohésion du collage se détériore. Et surtout, il y a une mise en œuvre raisonnable en ce qui concerne les coûts, le processus de production et la technologie des machines utilisées.
La technologie des machines utilisées, en particulier la technologie de dosage, apporte aussi son lot d’exigences. En ce qui concerne les types de construction, cela signifie qu’une attention particulière doit être accordée à la relation entre la surface adhésivée, l’épaisseur et l’état de surface. Il est également important de se demander : Le processus nécessite-t-il un prétraitement des surfaces ? Ou d’autres méthodes d’assemblage sont-elles nécessaires en plus – en ce qui concerne les forces de pression de contact, le temps de pressage, etc.
L’une des plus grandes différences entre la réalisation d’un système à un composant et celle d’un système à deux composants est l’effort de nettoyage nécessaire. Les temps de purge doivent être strictement respectés pendant le process. Un autre point non négligeable est le besoin d’espace plus important. Les coûts d’acquisition sont également plus élevés pour les systèmes à deux composants.
En général, cela s’applique à toutes les industries : Le rapport de mélange des adhésifs à deux composants doit être strictement respecté. Un dosage absolument précis est nécessaire. Même si, par exemple, dans le secteur automobile ou électronique, la tolérance sur la quantité totale est généralement plus faible.
Une différence majeure entre les différents secteurs d’industrie dans lesquels la technologie de collage est utilisée reste le degré d’automatisation du système, en particulier, la capacité de récupérer et d’enregistrer divers paramètres pertinents pour le processus via un logiciel. La traçabilité complète, à savoir quel composant a été appliqué, quand et avec quels paramètres, ne peut être réalisée que dans un système entièrement automatisé. Le collage dans les secteurs de l’électronique et de l’automobile est beaucoup plus critique que, par exemple, le collage des conduits de ventilation, des panneaux en bois ou autres.
Les sources d’erreurs récurrentes, comment les éviter ?
En raison d’un manque d’information préalable ou d’une connaissance insuffisante du processus, les problèmes apparaissent parfois très tard. Ils ne peuvent alors souvent être résolus qu’à grands frais. Souvent, tant le client final que le fabricant de la machine ne disposent pas des connaissances nécessaires et d’une expérience suffisamment importante : ils ne sont pas conscients qu’un manque d’information ou de supposés « petits changements » dans le suivi ou dans le projet en cours peuvent entraîner des modifications considérables du système de dosage afin d’obtenir un processus stable. Si, par exemple, la quantité effectivement dosée est inférieure ou supérieure à la quantité initialement prévue, cela signifie souvent qu’une autre tête de mélange est nécessaire. Ou, à court terme, vous pouvez décider d’utiliser un adhésif différent qui, dans le pire des cas, peut nécessiter un système de dosage complètement différent en raison de ses propriétés.
Même l’interaction de composants provenant de différents fabricants pose souvent des problèmes d’interface. Ou une autre erreur classique : le client final veut planifier et installer lui-même les tuyaux d’alimentation de colle. Des tuyaux trop fins et/ou trop longs sont alors souvent utilisés – et au final, il n’arrive pas assez de matière au système de dosage. À ce stade, la disposition est souvent déjà fixée et dans le pire des cas, par exemple, des axes linéaires plus grands, des robots ou similaires seraient nécessaires. Ou bien un système d’extraction ou d’alimentation devrait être plus proche des autres composants, mais cela n’est plus possible par manque de place.
Comment peut-on éviter ces problèmes ?
- Tout d’abord, le projet doit être clairement documenté. La documentation de tous les composants doit être complète et décrite de manière suffisamment détaillée. Insistez sur la remise de tous les documents nécessaires.
- Utiliser des systèmes autonomes lorsque cela est possible. Par exemple, il existe des fabricants d’adhésifs qui proposent des ensembles « tout en un » et garantissent ainsi la fonctionnalité. Ou s’appuyer sur des solutions qui ont été suffisamment testées en termes d’adéquation et de fiabilité des processus en coordination avec les fabricants de colles et de technologies de dosage.
- Demandez qu’un interlocuteur direct connaissant bien le projet soit en permanence disponible pour vous aider à répondre aux questions et aux demandes.
Structure possible d’un système de dosage bi-composants 2K :
Les points qu’il faut respecter lors de l’utilisation quotidienne des systèmes de dosage d’adhésifs :
- Ne laissez pas les adhésifs à l’air libre. Cela provoquerait l’évaporation des ingrédients, les propriétés des composants pourraient en être altérées et les adhésifs sensibles à l’humidité pourraient durcir partiellement ou complètement.
- Les fluides de dosage ne doivent pas être stockés trop longtemps pour éviter la sédimentation des charges – il est fortement recommandé de travailler selon le principe du premier entré, premier sorti.
- N’ajoutez pas d’air à la matière lorsque vous la remuez. L’objectif est d’obtenir un mélange totalement homogène. Les bulles d’air dans le produit à doser peuvent entraîner une réduction de la force d’adhésion. En cas de doute, un système de traitement du produit, c’est-à-dire de dégazage de l’adhésif, doit être installé en aval.
- Dans le cas des silicones de polyaddition à deux composants, il faut éviter à tout prix le transfert du catalyseur en platine au deuxième composant. Cela pourrait se produire, par exemple, si un seul outil est utilisé pour les deux composants – et cela conduirait au durcissement de la colle.
- Pour les silicones de polyaddition à 1 et 2 composants, il est important d’éviter la contamination du catalyseur par contact avec du soufre, une amine ou des composés organométalliques ou des plastifiants. La contamination peut être causée par l’utilisation de gants adaptés ou par des joints ou des tuyaux réticulés au soufre, par exemple. Il en résulterait un matériau trop mou et collant, voire parfois complètement liquide.
- L’utilisation de métaux (en particulier de métaux non ferreux) doit être évitée lors du traitement des adhésifs à durcissement anaérobie. Leur utilisation entraînerait une activation supplémentaire et donc un durcissement dans le système de dosage. Si l’utilisation de composants métalliques est absolument nécessaire, ils doivent être en acier inoxydable. Et ils devraient être en outre passivés – éventuellement même régulièrement, en fonction des cycles de production.
- En général, plus de durcisseur ne signifie pas automatiquement plus rapide ou plus rigide : pour de nombreux adhésifs, cela est même contre-productif (réaction de polyaddition). De même, dans les réactions de polymérisation, il n’existe qu’une plage limitée dans laquelle on peut modifier le rapport de mélange pour ajuster la réaction cinétique et les propriétés finales.
- Si des silicones et d’autres adhésifs et revêtements sont utilisés simultanément, le transfert doit être évité à tout prix pour éviter les problèmes d’adhérence.
Trois conseils importants pour pouvoir utiliser des adhésifs :
- Examiner les spécificités / fiches techniques
- Acclimater l’adhésif
- Utiliser des produits de nettoyage appropriés
La compétence par l’expérience
ViscoTec a plus de vingt ans d’expérience dans le domaine de la technologie du collage. Au cours de cette période, les applications ont été nombreuses et stimulantes, ce qui a souvent permis d’acquérir de nouvelles connaissances et un savoir-faire plus étendu. En conséquence, les spécialistes de la technologie de dosage offrent des conseils avisés – dans un large éventail de secteurs et de domaines d’application – sur tous les aspects de la technologie de collage.
Outre les conseils techniques, des essais de dosage et des séries de tests approfondis sont effectués dans notre propre centre technique. Toujours en étroite collaboration avec les clients et les fabricants d’adhésifs. ViscoTec s’est donné pour mission de déterminer la technologie de dosage la plus appropriée pour tous les clients. De nombreux systèmes de test sont disponibles pour effectuer les essais – de l’extraction, à la préparation et au dosage ou à l’application de matériaux à un ou deux composants.
Au fil du temps, les experts de ViscoTec ont mis en place un vaste réseau et travaillent avec succès depuis des décennies avec les fabricants d’adhésifs les plus réputés du monde entier. Nous investissons en permanence dans de nouvelles technologies et dans des développements innovants.
Que vous ayez besoin d’informations sur les limites d’application, sur les erreurs possibles lors du développement ou du fonctionnement, ou que vous ayez des questions sur le dosage dans des environnements spécifiques, par exemple sous vide – ViscoTec se fera un plaisir de vous conseiller.