Fabrication additive à partir de matières liquides
Évaluation de différents procédés de fabrication additive avec des liquides et des pâtes
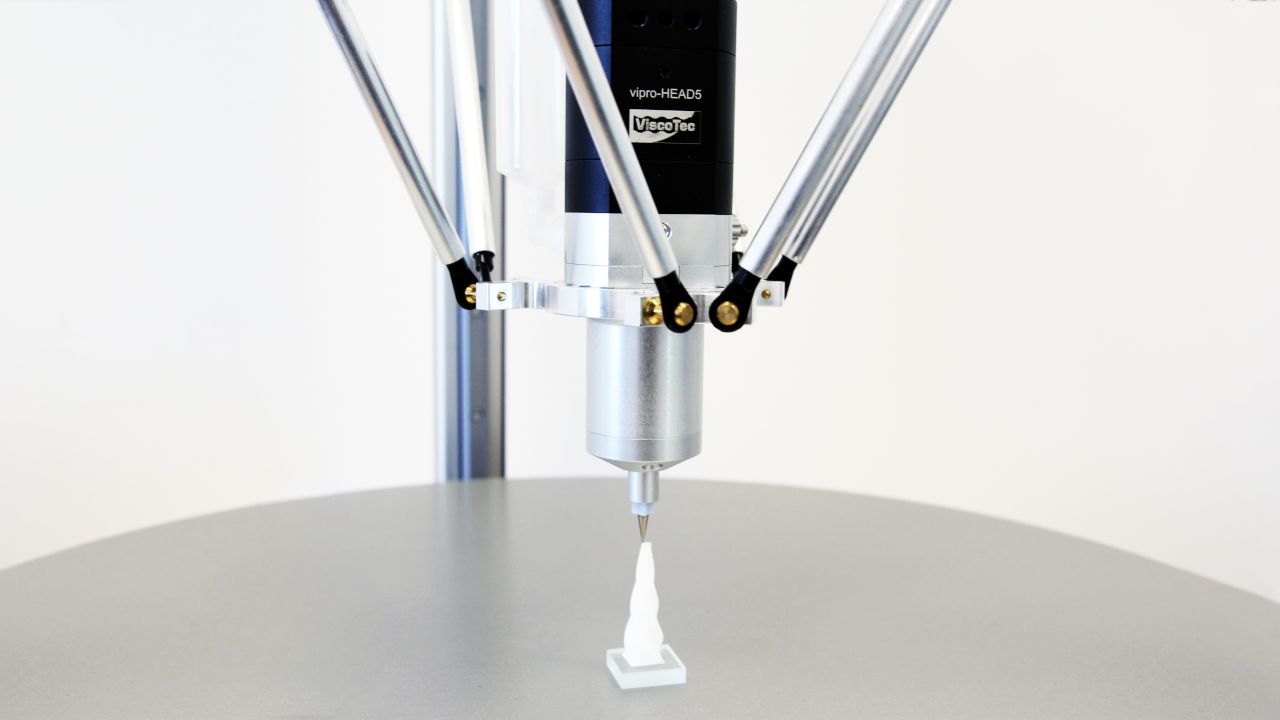
Les procédés de fabrication additive s’imposent de plus en plus dans les applications industrielles, car ils offrent des avantages significatifs aux clients par rapport aux procédés conventionnels. La fabrication additive est basée sur la structure en couches d’un composant. Le temps de production dépend donc du volume du composant à appliquer. La forme géométrique des différentes couches n’a qu’une influence mineure. Il en résulte une plus grande liberté de conception, sans que des étapes supplémentaires, telles que l’usinage, n’entraînent un surcroît de temps et de coûts. Ce procédé est particulièrement adapté à la production de composants géométriquement complexes, tels que les structures bioniques. Le processus qui va du fichier CAO à la pièce finie est largement automatisé.
De cette manière, les premiers modèles de composants peuvent être produits en peu de temps et à faible coût. Ces avantages, et bien d’autres, ont permis à la fabrication additive de s’imposer dans de nombreuses applications industrielles. En particulier, les procédés à base de poudre (comme le frittage sélectif au laser) et de fusion (comme la modélisation par dépôt fondu) sont utilisés, par exemple, pour la production de prototypes, mais aussi pour des composants en série.
Les procédés de fabrication additive sont basés sur l’extrusion de liquides. Ce domaine n’en est encore qu’à ses débuts, mais se développe actuellement rapidement. En particulier, le grand nombre de nouveaux matériaux pour l’impression 3D crée un grand potentiel pour ces applications. Il s’agit, par exemple, du silicone (voir figure 1), des résines ou des pâtes métalliques.
Ce livre blanc étudie les technologies existantes pour la fabrication additive de composants à partir de produits liquides. Les avantages et les inconvénients des différents procédés y sont présentés, ainsi que les différents paramètres de contrôle de chaque procédé pour modifier la quantité appliquée.
Les différents procédés de fabrication additive avec des liquides et des pâtes sont :
- le dispositif de dosage pneumatique
- le drop-on-demand (valve à jet)
- le principe du piston sans fin
Le dispositif de dosage pneumatique
Avec le dispositif de dosage pneumatique (méthode temps-pression), un contenant est mis sous une pression définie. Le liquide est expulsé par une force de pression appliquée au piston (voir figure 2).
Le paramètre de contrôle de ce système est la pression appliquée sur le liquide. En raison des fluctuations de température ou des propriétés thixotropiques du fluide, la viscosité peut changer en très peu de temps. Cette différence de viscosité, pour une même pression, se traduit par des quantités de fluide appliqué différentes.
Le système ne se distingue donc pas par sa stabilité de process et n’a pas une grande précision de répétabilité.
Les conditions fluctuantes du process (par exemple la température ou l’humidité) nécessitent une procédure de calibrage quotidienne. Qui plus est, la réaspiration souhaitée du produit (« Retract ») dans l’impression 3D n’est pas possible avec ce type de procédé, car la pression sur le fluide ne peut être que réduite.
Toutefois, la mise en œuvre du système est très rentable, car il s’agit d’un système simple avec peu de composants et sans mécanique complexe. En plus, le poids de la tête d’impression est faible par rapport aux autres têtes d’impression.
L’épaisseur minimale réalisable de la couche dépend de l’aiguille et peut être >0,2 mm dans des conditions de procédé idéales.
Le « Drop-On-Demand » (valve à jet)
Le système de Drop-On-Demand (de goutte à la demande) utilise une valve à jet pour évacuer le liquide. Semblable à la technologie d’une imprimante à jet d’encre, elle produit de très fines gouttelettes qui sont projetées sur une plateforme de fabrication. Il y a un espace d’air entre la valve et la plateforme de fabrication, de sorte qu’il n’y a pas de contact entre les deux. Les paramètres de contrôle pour l’application du produit sont le nombre de gouttelettes par unité de temps et la taille des gouttelettes. La technologie « BubbleJet » ou « piezo » est généralement utilisée pour générer les gouttelettes. Dans le procédé BubbleJet, un élément chauffant génère une bulle de vapeur locale, qui déplace la matière par son changement de taille volumétrique et émet ainsi une gouttelette.
Dans les valves piézoélectriques, un cylindre est déplacé par l’effet piézo inverse, qui éjecte une goutte, comme le montre la figure 3. La fréquence de gouttelettes réalisable est d’environ 23 kHz.
Selon le fluide appliqué avec la valve à jet, il existe différents noms pour ces procédés :
- L’un des premiers procédés historiques utilisant une valve à jet est le » Binder Jetting « . Ici, un liant liquide est introduit dans un lit de poudre. Entre chaque couche, une raclette se déplace sur le lit de poudre et applique la couche de poudre sur le composant et l’espace d’assemblage. La tête d’impression dose le liant aux endroits souhaités et solidifie ainsi la poudre. Ce procédé peut être utilisé pour produire des composants à partir d’une large gamme de matériaux en poudre, tels que l’amidon, le plâtre, l’aluminium et le plastique. Si le liant est coloré, des composants avec n’importe quel dégradé de couleur sont possibles. Qui plus est, aucune structure de support n’est nécessaire, car le lit de poudre soutient le composant. Certains matériaux nécessitent un post-traitement au four (frittage) pour obtenir une plus grande résistance.
- Un autre système de drop-on-demand est la procédure « PolyJet » (« Material Jetting »). Au lieu du liant, on utilise un polymère photosensible. Le composant est constitué du polymère, qui est jeté directement sur le lit d’impression. Par conséquent, aucune poudre n’est nécessaire comme dans le cas du Binder Jetting. Chaque couche appliquée doit être durcie à la lumière UV.
- Un procédé récemment mis au point permet la projection de silicones et donc la production de composants en silicone selon le principe de drop-on-demand. Comme pour le procédé PolyJet, le composant est durci par la lumière UV après chaque couche.
Un avantage majeur des têtes d’impression à jet est la haute résolution qui est liée à la taille des gouttelettes. Cela signifie que des épaisseurs minimales de revêtement allant jusqu’à 16 µm peuvent être atteintes avec des matériaux à faible viscosité. Il en résulte une très grande qualité de surface où l’effet d’escalier est à peine perceptible. Si l’on utilise du silicone à haute viscosité, la plus petite résolution possible actuellement est de 0,1 mm.
Lors de la génération des gouttelettes, un apport énergétique élevé est localement introduit dans le fluide. Les forces de cisaillement qui en résultent peuvent être nocives pour certains matériaux. Tous les systèmes basés sur une vanne à jet présentent un inconvénient : le fluide doit être ajusté avec précision au système pour que l’application des gouttelettes fonctionne comme souhaité. Cela signifie qu’aucun matériau standard ne peut être utilisé, mais que des fluides spécialement adaptés doivent être traités. Ces matériaux spéciaux sont pour la plupart très coûteux.
Le principe du piston sans fin
La pompe à cavité progressive, également connue sous le nom de principe du piston sans fin, est une pompe volumétrique rotative.
Le système se compose d’un rotor, qui est conçu comme une vis à filetage rond à grand pas et à grande profondeur. Le stator élastique a un double filetage et une longueur de pas double de celle du rotor. Cette géométrie se traduit par des chambres fermées d’un volume également défini entre le rotor et le stator, qui sont entraînées vers l’avant par le mouvement du rotor. En raison des chambres fermées, la pompe est étanche, il n’est donc pas nécessaire de prévoir une vanne à l’entrée et à la sortie. Le débit de matière est volumétrique et directement proportionnel à l’angle de rotation du rotor.
En combinant deux pompes, il est également possible de traiter des matériaux à deux composants. Les deux matériaux sont chacun transportés par une pompe dans un mélangeur statique où ils sont mélangés. Le rapport de mélange est librement sélectionnable et peut être ajusté pendant le process de production.
Par rapport aux autres têtes d’impression, la conception du stator et du rotor donne un dessin relativement long. Contrairement au système temps-pression, les exigences de qualité élevées imposées aux composants de la pompe à vis excentrée entraînent des coûts relativement élevés, qui restent toutefois inférieurs à ceux d’un système de « drop-on-demand ».
En transportant le fluide dans les chambres, des forces de cisaillement très faibles sont générées, ce qui rend le système adapté aux milieux sensibles au cisaillement.
Un point essentiel de la fabrication additive est la réaspiration de la matière (« Retract »). Le sens de rotation de la vis est ainsi inversé et le produit est renvoyé dans la pompe. Cela crée une rupture de fil net. On évite ainsi tout écoulement indésirable de produit.
Un autre avantage majeur est la variété des matériaux qui peuvent être traités avec ce principe. Il s’agit notamment de fluides de faible à très haute viscosité, de liquides à forte teneur en charges, de matériaux sensibles à la température et de fluides abrasifs. Parmi les exemples concrets déjà utilisés, on peut citer les silicones, les polyuréthanes, les résines époxy et les céramiques.
En raison de la géométrie particulière du rotor et du stator, le fluide est transporté sans pulsation, ce qui se traduit par une largeur constante des cordons générés et un contour extérieur uniforme.
Grâce au dosage volumétrique, l’adaptation aux différents diamètres de buse est très facile. Le plus petit diamètre intérieur des buses est actuellement de 0,2 mm. Il est donc possible d’obtenir des épaisseurs de couche de <0,2 mm.
En Résumé
Il faut dire que les différents procédés de fabrication additive avec des liquides ont tous des avantages et des inconvénients différents. Le choix du procédé le plus approprié dépend des propriétés requises du composant.
- Un système temps-pression peut être la solution la plus efficace pour appliquer des liquides sur le lit d’impression avec une faible viscosité et des exigences moindres en matière de qualité des composants.
- Pour une exigence élevée de détail, les systèmes de « drop-on-demand » sont très adaptés.
- L’avantage de la pompe à cavité progressive est la très grande précision de dosage, le traitement des matériaux bi-composants 2K et la très large gamme de fluides traitables.
Auteur: Simon Kasböck, Business Development Additive Manufacturing